Introduction
The medical device industry operates under a stringent regulatory environment, where the role of a Quality Manager is paramount in ensuring compliance and product excellence. This position not only involves the development and maintenance of robust Quality Management Systems (QMS) but also encompasses critical responsibilities such as:
- Conducting audits
- Managing non-conformances
- Fostering a culture of quality through effective training and mentorship
As the landscape of medical devices evolves, particularly with the advent of technologies like the Internet of Medical Things (IoMT), Quality Managers must navigate complex regulatory requirements while integrating advanced quality practices. This article delves into the essential responsibilities, skills, and strategies that define the role of Quality Managers in this dynamic field, highlighting their impact on product safety and efficacy.
Key Responsibilities of a Quality Manager in Medical Devices
The role of a quality manager medical device in the industry is crucial to ensuring that assurance processes are effectively implemented throughout the product lifecycle. This role includes several essential duties:
- Developing Management Systems for Excellence (MSE): A Quality Manager must create and uphold a strong MSE that complies with regulatory requirements, ensuring effective control and assurance practices. Comprehensive instruction on QMS guidelines, such as ISO 9001, is crucial for meeting requirements and improving overall management. Instructing staff on these guidelines aids in guaranteeing adherence and enhancing overall management of excellence.
- Conducting Audits and Inspections: Regular internal evaluations and involvement in external inspections are essential for measuring conformity with established benchmarks. Recent data indicates that companies with rigorous audit processes have higher compliance rates, demonstrating the effectiveness of such measures in maintaining standards.
- Managing Non-Conformances: Identifying, documenting, and addressing non-conformances in product performance is a key responsibility. Implementing corrective and preventive actions (CAPA) is vital to avoid repetition and guarantee ongoing enhancement.
- Training and Mentorship: A Quality Manager plays a key role in instructing personnel on excellence criteria and practices, thereby nurturing a culture of excellence within the organization. This is increasingly important as the industry shifts towards more complex technologies, such as the Internet of Medical Things (IoMT), which require skilled professionals to navigate emerging challenges, including cybersecurity. The IoMT technologies are essential for decreasing healthcare expenses and delivering personalized care through data gathering and remote observation, but they also present cybersecurity issues, highlighting the requirement for proficient cybersecurity experts.
- Collaboration with Cross-Functional Teams: Working together with research and development, manufacturing, and regulatory teams ensures that standards are integrated throughout the product development and commercialization phases. In accordance with Lean and Six Sigma approaches, which target a defect rate of 3.4 per million opportunities, this partnership is crucial for attaining high standards of product quality.
In summary, the responsibilities of a quality manager medical device are critical not only for adherence but also for improving the overall quality management structure within medical equipment organizations.
Essential Skills and Qualifications for Quality Managers in Medical Devices
The role of quality manager medical device in the industry requires a specific set of essential skills and qualifications to ensure adherence and product excellence. This is exemplified by leaders like Ana Criado, our Director of Regulatory Affairs, whose extensive experience at INVIMA equips her with a deep understanding of the regulatory landscape. Her academic background as a biomedical engineering professor further enriches her capability to address the technical challenges that Quality Managers face.
Similarly, Katherine Ruiz’s expertise in Regulatory Affairs for Medical Devices and In Vitro Diagnostics in Colombia highlights the critical knowledge necessary to navigate complex regulatory requirements and ensure product compliance.
- Educational Background: A minimum of a bachelor’s degree in engineering, life sciences, or a related field is generally required, with many employers favoring candidates with a master’s degree for advanced knowledge and expertise. For instance, Ana's master's degree in health economics & pharmacoeconomics provides her with insights into the economic implications of management decisions.
- Certifications: Professional credentials, such as the Certified Quality Engineer (CQE) and ISO 13485 Lead Auditor certifications, are highly regarded in this field, signaling a commitment to management excellence. These certifications prepare quality manager medical device professionals to implement and oversee assurance systems effectively.
- Regulatory Knowledge: A thorough understanding of FDA regulations, ISO standards, and international standards is crucial. As emphasized by the FDA, "employees performing functions within the realm of the Quality System Regulations for medical devices must be trained as such, and documentation of that training is a cGMP requirement." This highlights the need for rigorous training documentation, as discussed in the case study titled "Acceptable vs. Unacceptable Training Documentation." This case study details acceptable types of documentation, stressing that only particular forms, such as certificates of completion and signed attendance sheets, are valid proof of training, which is crucial for adherence and responsibility in management roles.
- Analytical Skills: Strong analytical abilities are essential for effectively interpreting complex data and making informed decisions that affect product standards and compliance. Both Ana and Katherine exemplify these skills through their ability to analyze regulatory changes and their implications for product development.
- Leadership and Communication: Effective leadership and communication abilities are essential for managing teams and fostering collaboration among diverse stakeholders within the organization. Ana's leadership in Regulatory Affairs illustrates the significance of clear communication in ensuring that quality criteria are met across departments.
Moreover, continuous professional development is crucial for a quality manager medical device to stay updated with the latest industry standards and practices. This combination of educational qualifications, certifications, regulatory knowledge, analytical prowess, and interpersonal skills is essential for a successful career as a quality manager medical device in the medical sector.
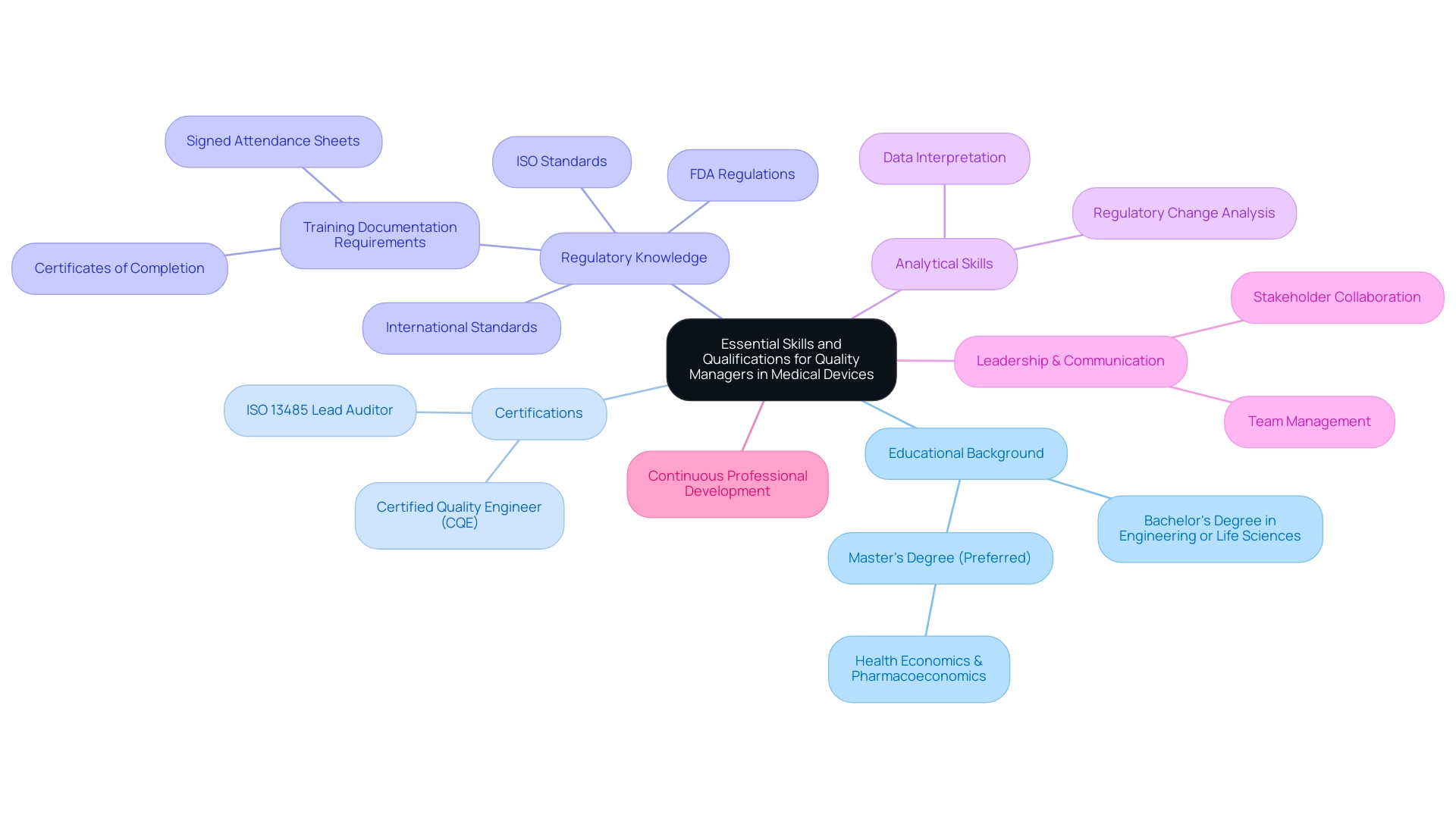
Navigating Regulatory Compliance in Medical Device Quality Management
Navigating regulatory adherence is a cornerstone of responsibility for the quality manager medical device in the medical equipment sector. Several key elements are crucial for successful adherence:
- Understanding ISO 13485: This standard outlines the requirements for a robust management system tailored to medical devices, with a strong emphasis on risk management and process control. Following ISO 13485 not only aids in meeting standards but also enhances overall product quality and safety. For instance, VSE builds electronics that adhere to ISO 13485 certification, showcasing a practical application of regulations in the industry.
- FDA Regulations: Adherence to FDA regulations, especially 21 CFR Part 820, is an essential requirement for ensuring the safety and efficacy of medical products. A quality manager medical device must remain vigilant and informed about evolving regulations and accompanying guidance documents to navigate these waters effectively.
- Documentation and Record-Keeping: Comprehensive documentation plays a vital role in demonstrating adherence during audits and inspections. This involves the careful upkeep of design history files, device master records, and performance records, which collectively offer a clear perspective of the regulatory environment.
- Training and Awareness: Implementing ongoing training programs for staff regarding regulatory requirements and performance standards is vital in fostering a culture of adherence within the organization. Such initiatives not only improve understanding but also enable employees to contribute positively to the regulatory framework.
- Integrating ISO 14971 Risk Management Principles: Best practices for integrating ISO 14971 risk management principles within the new QMSR framework are essential for identifying and mitigating risks throughout the product lifecycle. This proactive approach ensures that quality management systems are not only compliant but also resilient against potential failures. Furthermore, as highlighted in the 2023 Thomson Reuters Risk & Governance Survey Report, a significant 77% of corporate risk and regulatory professionals emphasize the importance of staying updated on the latest developments related to environmental, social, and governance (ESG) factors. This increasing acknowledgment highlights the importance for the quality manager medical device to incorporate ESG factors into their regulatory strategies. The case study titled 'Importance of ESG Updates' illustrates that 77% of corporate risk and regulatory professionals value staying informed on these developments, reinforcing the need for a quality manager in the medical device industry to align their practices with broader industry trends.
Adding to this landscape, Ana Criado, our Director of Regulatory Affairs, brings extensive expertise in biomedical engineering and regulatory compliance, having served in leadership roles at Colombia’s INVIMA. With her background as a professor and consultant for global companies, she emphasizes the importance of regulatory knowledge in navigating the complex medical landscape, particularly in relation to cannabis regulation at Mahu Pharma. Ana holds a degree in chemical pharmacology, a master's degree in health economics & pharmacoeconomics, and certifications in clinical epidemiology, good clinical practices & study monitoring, and pharmacovigilance, which further solidify her qualifications in the field.
The Role of Post-Market Surveillance in Quality Management
Post-market monitoring is crucial for the quality manager medical device to uphold high-quality criteria in medical products, especially within the regulatory structure set by INVIMA (Colombia National Food and Drug Surveillance Institute). INVIMA, established in 1992, plays a vital role in inspecting and overseeing health products, which includes the responsibilities of a quality manager medical device to ensure adherence to safety and efficacy criteria essential for medical devices. Its multifaceted role encompasses several critical functions:
- Monitoring Product Performance: Systematic collection and analysis of data on product performance and user feedback are crucial for identifying potential safety issues and pinpointing areas for improvement.
This proactive approach aligns with the ISO/TR 20416:2020 guideline, which emphasizes that questionnaires must be understandable, validated, and distributed to a representative sample of the target population. As Enrico Perfler states, 'For this purpose, the ISO/TR 20416:2020 standard provides guidelines, specifying in particular that questionnaires must be designed to be understandable and easy to complete, validated to ensure accurate measurement of the desired aspects, and distributed to a representative sample of the target population.'
- Adverse Event Reporting: Establishing robust procedures for reporting adverse events is vital for ensuring compliance with regulatory requirements, particularly for devices classified under the IVDR as Class C and D, which necessitate a periodic safety update report (PSUR).
This requirement underscores the importance of a quality manager medical device for thorough monitoring and reporting mechanisms in light of INVIMA's oversight, which is classified as a Level 4 health authority by PAHO/WHO.
- Continuous Improvement: Utilizing surveillance data to implement corrective actions demonstrates a commitment to ongoing excellence enhancement. Addressing challenges, such as those related to the integration of large language models (LLMs), is crucial for maintaining the accuracy and reliability of safety evaluations.
The case study titled 'Challenges in Applying LLMs for Postmarketing Surveillance' highlights that while LLMs offer significant potential for improving postmarketing surveillance, there are several challenges, including the need for extensive infrastructure and the risk of generating inaccurate outputs. This illustrates the importance of aligning such technologies with INVIMA's regulatory framework to ensure effective post-market surveillance practices.
- Stakeholder Communication: Engaging effectively with stakeholders—including healthcare providers and patients—facilitates the gathering of insights and the addressing of concerns regarding product performance. This two-way communication helps in understanding user experiences and expectations, which are integral for refining product quality.
In summary, the dynamic nature of post-market surveillance, including the latest trends and the necessity for comprehensive adverse event reporting systems, is vital for a quality manager medical device to ensure the ongoing safety and efficacy of medical products in the healthcare landscape, supported by INVIMA's rigorous regulatory framework. Furthermore, the quality manager medical device ensures that the Directorate for Medical Equipment and other Technologies plays a crucial role in overseeing these processes, guaranteeing that all medical products meet the required standards for safety and efficacy.
Leveraging Technology for Enhanced Quality Management in Medical Devices
Utilizing technology is essential for a quality manager in the medical device sector to improve management standards. Significant advancements include:
- Management Software: The implementation of specialized software solutions not only streamlines processes but also enhances documentation management and facilitates audits. Companies like Microsoft and Oracle are at the forefront of this trend, showcasing how effective QMS tools can optimize operations. In 2024, North America was the largest region in the management software market, reflecting the growing demand for these solutions in the medical device sector.
- Data Analytics: The integration of data analytics tools allows organizations to analyze performance metrics rigorously and identify emerging trends. This proactive strategy assists in informed decision-making, ultimately resulting in improved product standards. Recent statistics indicate a significant uptick in the adoption of data analytics within performance management, highlighting its growing importance.
- Training on QMS Standards: Training employees on QMS standards, such as ISO 9001, is essential for ensuring compliance and enhancing overall management. This investment in human capital is essential for sustaining enhancements and meeting regulatory requirements.
- Automation of Processes: Automating routine assessments and documentation procedures significantly reduces human error and enhances overall efficiency. This trend towards automation is transforming how quality manager medical device roles are approached in the medical device sector.
- Digital Collaboration Tools: The use of digital tools promotes cooperation among cross-functional teams, ensuring that excellence considerations are seamlessly integrated throughout the product lifecycle. As management standards evolve, the significance of such collaborative technologies cannot be overstated, positioning companies to better meet regulatory requirements and enhance product outcomes.
- Case Studies: Major companies in the management software market, including Microsoft and Oracle, leverage their technological capabilities to capture a significant share of the expanding QMS market. Their innovative solutions and commitment to being a quality manager medical device set benchmarks for the industry, illustrating how technology can drive quality improvements in medical devices.
Conclusion
The role of a Quality Manager in the medical device industry is integral to maintaining compliance and ensuring product excellence. Through the development and implementation of robust Quality Management Systems (QMS), these professionals navigate complex regulatory landscapes, conduct thorough audits, and manage non-conformances. The emphasis on a culture of quality, fostered through effective training and mentorship, is crucial as the industry embraces advanced technologies like the Internet of Medical Things (IoMT).
Essential skills for Quality Managers include:
- A solid educational foundation
- Relevant certifications
- A deep understanding of regulatory requirements
The ability to analyze data and communicate effectively across teams enhances their capacity to uphold quality standards. Moreover, staying abreast of evolving regulations and integrating best practices in risk management are vital for successful compliance.
Post-market surveillance, a critical aspect of quality management, ensures ongoing safety and efficacy of medical devices. By collecting performance data and establishing robust reporting mechanisms, Quality Managers can drive continuous improvement and maintain high-quality standards. The incorporation of technology, such as quality management software and data analytics, further enhances these efforts, streamlining processes and facilitating informed decision-making.
In conclusion, the multifaceted responsibilities of Quality Managers not only safeguard compliance but also elevate the overall quality framework within medical device organizations. Their strategic approach to quality management, combined with a commitment to continuous improvement and the adoption of innovative technologies, positions the industry for future success, ultimately ensuring the safety and efficacy of medical devices for patients worldwide.
Frequently Asked Questions
What is the role of a quality manager in the medical device industry?
The quality manager's role is crucial for ensuring effective assurance processes throughout the product lifecycle, which includes developing management systems, conducting audits, managing non-conformances, providing training, and collaborating with cross-functional teams.
What are the essential duties of a quality manager in medical devices?
Essential duties include developing Management Systems for Excellence (MSE), conducting audits and inspections, managing non-conformances, providing training and mentorship, and collaborating with cross-functional teams.
Why is developing Management Systems for Excellence (MSE) important?
Developing MSE is important to ensure compliance with regulatory requirements and effective control and assurance practices, which enhance overall management and adherence to quality standards.
How do audits and inspections contribute to quality management?
Audits and inspections help measure conformity with established benchmarks, and companies with rigorous audit processes tend to have higher compliance rates, demonstrating their effectiveness in maintaining standards.
What is the process for managing non-conformances?
Managing non-conformances involves identifying, documenting, and addressing issues in product performance, along with implementing corrective and preventive actions (CAPA) to avoid recurrence and ensure continuous improvement.
What role does training and mentorship play in quality management?
Training and mentorship are vital for instructing personnel on quality criteria and practices, fostering a culture of excellence and equipping staff to handle emerging challenges, especially with complex technologies like the Internet of Medical Things (IoMT).
How does collaboration with cross-functional teams benefit product quality?
Collaboration with teams such as research and development, manufacturing, and regulatory ensures that quality standards are integrated throughout the product development and commercialization phases, aiming for high product quality.
What qualifications are typically required for a quality manager in the medical device field?
A quality manager typically requires a bachelor's degree in engineering, life sciences, or a related field, with many employers favoring candidates with a master's degree. Professional certifications like Certified Quality Engineer (CQE) and ISO 13485 Lead Auditor are also highly regarded.
Why is regulatory knowledge important for a quality manager?
A thorough understanding of FDA regulations, ISO standards, and international standards is crucial for ensuring product compliance and effective management of quality systems within the medical device industry.
What skills are essential for a successful quality manager in medical devices?
Essential skills include strong analytical abilities, effective leadership and communication skills, and a commitment to continuous professional development to stay updated with the latest industry standards and practices.
List of Sources
- Key Responsibilities of a Quality Manager in Medical Devices
- Ranking the 5 Best Quality Management System Software in 2024 (https://abiresearch.com/blog/best-quality-management-system-qms-software)
- Quality Management Systems Statistics 2025 (https://llcbuddy.com/data/quality-management-systems-statistics)
- Medical Quality Management Systems QMS Market Report 2025, Market Size, Share, Growth, CAGR, Forecast, Revenue (https://cognitivemarketresearch.com/medical-quality-management-systems-qms-market-report?srsltid=AfmBOoqJIRlu4VN3vSan4Wks9ouGmUpL3iRwLfpLPJlmun7BE5sYpCMC)
- 2024 Medical Device Industry Trends - Quality Manufacturing (https://mastercontrol.com/resource-center/quality-manufacturing/medical-device-industry-trends-2024)
- Essential Skills and Qualifications for Quality Managers in Medical Devices
- Medical and Health Services Managers (https://bls.gov/ooh/management/medical-and-health-services-managers.htm)
- A Guide for Managers: Employee Training Requirements for Medical Device and IVD Companies – Oriel STAT A MATRIX – ELIQUENT Life Sciences Blog (https://orielstat.com/blog/managers-guide-employee-training-requirements-for-medical-device-and-ivd-companies)
- Quality Control Manager Education Requirements in 2025 - Do You Need a Degree? (https://tealhq.com/education/quality-control-manager)
- Navigating Regulatory Compliance in Medical Device Quality Management
- ISO 13485 Certification: 2024 Update (https://linkedin.com/pulse/iso-13485-certification-2024-update-jeff-trambley-uefce)
- Most Popular Medical Device Content in 2024 (https://greenlight.guru/blog/most-popular-medical-device-content-2024)
- complianceandrisks.com (https://complianceandrisks.com/blog/24-stats-every-chief-compliance-officer-should-know-in-2024)
- The Role of Post-Market Surveillance in Quality Management
- Post-Market Surveillance for Medical Devices: Ultimate 2024 Guide | Sternum IoT (https://sternumiot.com/iot-blog/post-market-surveillance-for-medical-devices-regulations-and-plan-requirements)
- Enhancing Postmarketing Surveillance of Medical Products With Large Language Models (https://jamanetwork.com/journals/jamanetworkopen/fullarticle/2822418)
- Post-Market Surveillance for Medical Devices & IVDs: Requirements & Proactive Data Collection (https://greenlight.guru/blog/post-market-surveillance-medical-devices-ivds)
- Leveraging Technology for Enhanced Quality Management in Medical Devices
- Healthcare Quality Management Software Industry and Market Analysis Report 2025 (https://thebusinessresearchcompany.com/report/quality-management-software-global-market-report)
- Quality Management Systems Statistics 2025 (https://llcbuddy.com/data/quality-management-systems-statistics)
- Quality Management Software Market Size, Share and Forecast to 2033 (https://straitsresearch.com/report/quality-management-software-market)